What is a torque wrench?
Torque wrenches have been around for almost 100 years, giving us a means of reliably measuring the amount of force applied to a fastener (e.g. a nut or bolt). They’re precision measuring tools and generally accept standard sockets (e.g. 1/4″, 3/8″, 1/2″ etc.) and come in a range of sizes all the way up to 1m+ long wrenches for working on heavy machinery.
Why do you need a torque wrench?
Every bolt on your car or motorcycle has a correct torque setting; too little and the fastener might vibrate free, too much and you might break the fastener or something else. Some bolts are more well known for needing a correct torque, such as engine head bolts. Many people will say that they don’t need one and tighten bolts by feel – you certainly do get a feel over time, and using a torque wrench is a great way to safely develop that feel.
Different types of torque wrench
We’re looking at two types here so far – more to come as we acquire more types of torque wrenches.
Micrometer type
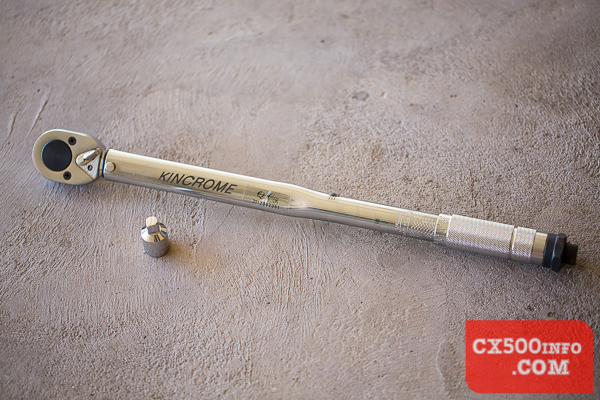
This is likely the most common type of torque wrench you will find, with prices for a basic 3/8″ drive unit ranging from absolute bottom basement level (~$20-25) to $100+. This type of torque wrench has several advantages; it is usually reversible – meaning that you can use it to measure torque when either tightening or loosening a bolt or when doing up left hand threaded bolts. They often have ratchet heads – something of an advantage when compared to having to lift the socket off the fastener, reposition and re-attach the socket. Micrometer type torque wrenches also generally self-reset, meaning you don’t have to remember to push a pin back in to re-enable the signal mechanism.
Due to the use of a spring in it’s mechanism, however, these can be more prone to going out of calibration than other torque wrench types. You also have to remember to relieve the spring when the torque wrench is not in use – generally resetting the wrench to zero or a low torque figure – to avoid loss of calibration.
Deflecting beam type
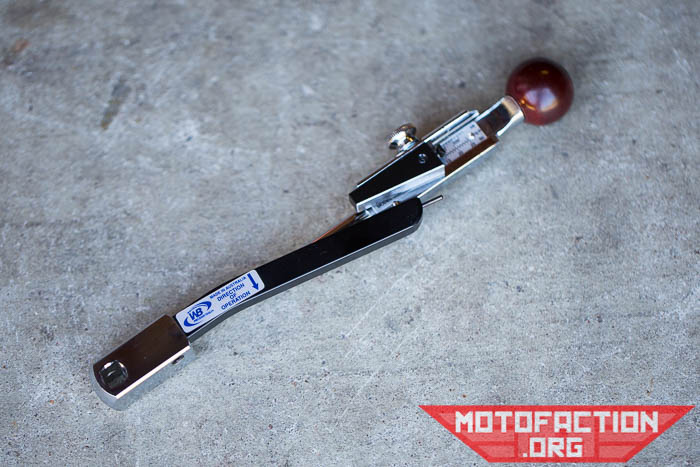
This type is an Australian invention! Rather than using a spring to measure the torque it uses a metal beam – meaning that there’s no wearing parts, and you don’t need to remember to reset it after use to prevent it from going out of calibration. They generally feature two signals when torque is reached – visible and audible, e.g. you can see the pin shoot out and you can also hear the distinctive “click”. The visible signal is handy for noisy environments and the audible trigger means that the torque wrench can be out of sight and still be useful – very handy when it’s deep in an engine bay.
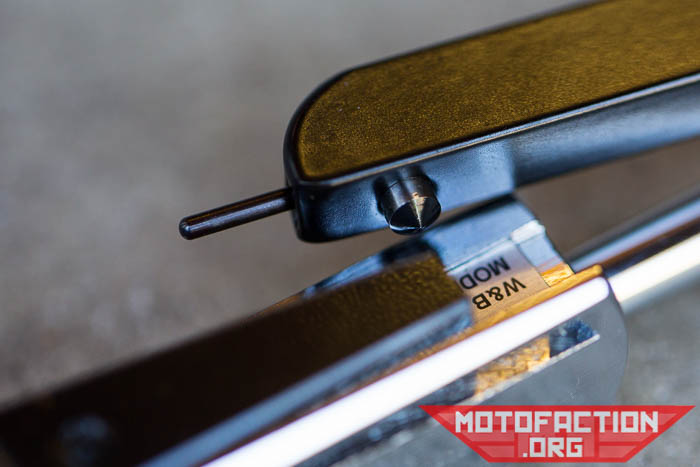
One downside is that you have to remember to push the pin back in to prime it for the next reading – if you forget to do so you won’t get a signal at all. Deflecting beam torque wrenches also generally don’t feature ratcheting heads, though ratcheting adapters do exist. They’re often more expensive than micrometer type torque wrenches, though that could be that there doesn’t seem to be any really budget options available… which may not be a bad thing. They can also only read torque in one direction, which isn’t a problem for most automotive work but could be a dealbreaker for some specific applications.
What to look for in a torque wrench
Range and accuracy! Every torque wrench has a usable range – e.g. 10 to 150 ft-lb – and a stated accuracy, e.g. 4%. If you are working primarily on one vehicle, read through the service manual and see what the typical torque values are and which torque measurement is used. If you buy a torque wrench that only displays in ft-lb and kg-m and your service manual only uses N·m, you’ll be doing a conversion every time you want to use it which will get tiresome quickly. It might be that a single torque wrench can fulfil all of the needs – e.g the above mentioned 10 to 150 ft-lb – or it might be that a pair of wrenches is a good fit, such as a 3/8″ drive for most fasteners and a 1/4″ drive for the smaller ones.
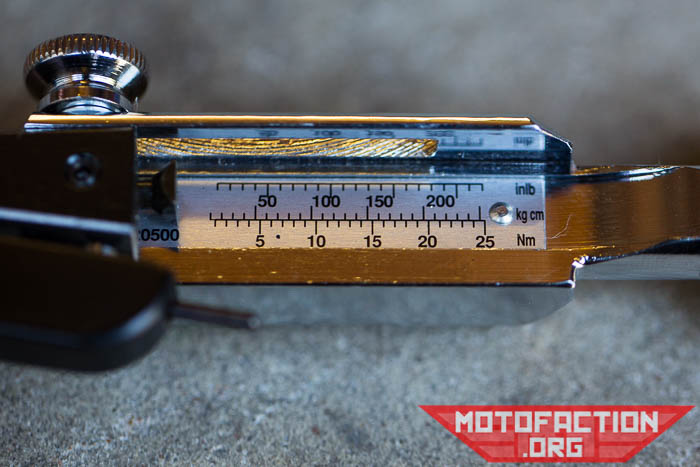
Also look at the highest torque value required – some vehicles will have a couple of outliers, such as flywheel bolts or single sided swingarm bolts. If they’re the kind of fastener that you only need to touch rarely it might be more cost effective to borrow a tool from a friend for that one job.
Do I really need one?
In our opinion, absolutely. We’ve seen many issues – from brake caliper bolts falling out due to not being torqued enough to cracked engine casings from a sump plug being over-torqued – which would have almost certainly been avoided through the use of a torque wrench. You might find that you use it less over time as you develop more of a feel, but we strongly feel that it’s a necessary part of your tool kit and will be useful on any vehicle you work on. Definitely don’t buy one as one of your first tools – a good set of sockets etc. should be a prior purchase – but even an inexpensive micrometer type is much better than nothing when it comes to developing a feel for how tight you should be doing up your fasteners.
So what does MotoFaction buy?
Keeping in mind that we are working on engines every single week of the year, we favour the deflecting beam type. No spring to remember to release tension on, and we are banking on the likelihood that the deflecting beam type is less likely to lose calibration over time than the micrometer spring-type… and what good is an innaccurate (or never tested) precision tool? Time and several rounds of calibration will tell whether that holds true but for now it’s deflecting beam type all the way – we don’t have to measure torque on left hand threads or loosening bolts, so those advantages of the micrometer type don’t really help us.